W pierwszym odcinku naszego tryptyku o technologiach recyklingu energetycznego dla zmieszanych odpadów tworzywowych, próbowałem zniechęcić Czytelników do pirolizy jako metody odzyskiwania z odpadów tworzywowych energii i paliw. W drugiej części wspomnianego cyklu przedstawione zostały inne niż piroliza metody produkcji energii i paliw z odpadów. A w odcinku trzecim powracamy do pirolizy i zastanowimy się, czy nie da się wprowadzić odpadów tworzywowych tam, gdzie piroliza jest od lat wykorzystywana z powodzeniem, czyli do rafinerii.
W rafineriach produkujących paliwa silnikowe z ropy naftowej procesy termicznego przekształcania frakcji węglowodorowej w celu uzyskania odpowiednich produktów znane są od dziesiątek lat. Historycznie rzecz biorąc, pierwszą instalacją używaną do przetwórstwa ropy naftowej była DRW, czyli Destylacja Rurowo-Wieżowa. Destylacja ropy naftowej jest procesem zachowawczym, tzn. z mieszaniny węglowodorów, jaką jest ropa naftowa, wydziela się tylko te, które mają odpowiednią temperaturę wrzenia. Nie zmienia ona składu chemicznego poddawanego obróbce surowca. Szybko się jednak okazało, że uzysk produktów paliwowych z DRW jest niewystarczający oraz że jakość tych paliw jest nie wystarczająca. Dodatkowo pojawiła się duża ilość odpadów w postaci ciężkiej pozostałości po destylacji, których nie umiano zagospodarować. Taka sytuacja sprzyja rozwojowi technologicznemu, więc dość szybko opracowano całą rodzinę technologii, w których produkt poddawany jest obróbce termicznej prowadzącej do kontrolowanego rozpadu długich łańcuchów węglowodorów na krótsze. Technologie te różnią się między sobą: rodzajem wsadu, temperaturą procesu, rodzajem katalizatora i dodatkiem substancji reagujących, ale w każdej rafinerii można spotkać przynajmniej kilka z nich (patrz tabela 1).
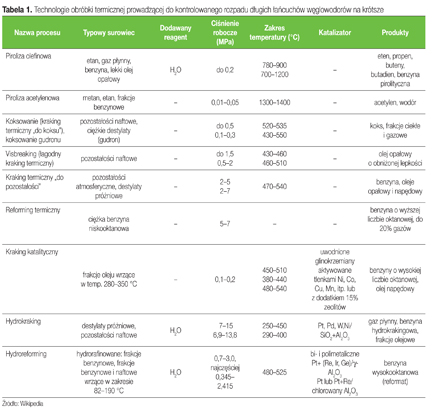
Pomimo tych różnic wspólną cechą technologii termicznej obróbki jest zamiana produktów ciężkich na produkty lekkie (gazowe i płynne). W przypadku tworzyw sztucznych mamy taką samą potrzebę: zamiany długich łańcuchów polimerów na krótkie łańcuchy paliw płynnych czy gazowych. Jak już wspomnieliśmy w pierwszym odcinku naszego tryptyku, tworzywa posiadają dużą lepkość w stanie stopionym i dużą zdolność do tworzenia koksu, co może spowodować uszkodzenie aparatury – na taki koksik, jako produkt, również nie ma zapotrzebowania.
Zamiana surowców wsadowych na tworzywa sztuczne w rafineryjnych procesach termicznych, bez modyfikacji aparatury i parametrów samego procesu to pewna katastrofa: przewody doprowadzające uległyby zakoksowaniu, wzrost ciśnienia rozerwałby aparaty, uwolnione w wybuchu gazy spowodowałyby pożar, obejmujący także sąsiednie instalacje. W skrócie: doskonały scenariusz na film katastroficzny.
Czy zatem mimo tak ponurych przewidywań nie udałoby się poprowadzić pirolizy tworzyw w rafinerii? Ależ udałoby się! Trzeba jednak zastosować jeden z dwóch schematów postępowania: albo zmodyfikować proces pirolizy i dostosować go do specyfiki tworzyw sztucznych jako surowca, a sam proces prowadzić w bliskiej kooperacji z innymi instalacjami (jak to jest realizowane na świecie powiem w dalszej części tego artykułu), albo odwołać się do mądrości znanego wszystkim uczonego Paracelsusa.
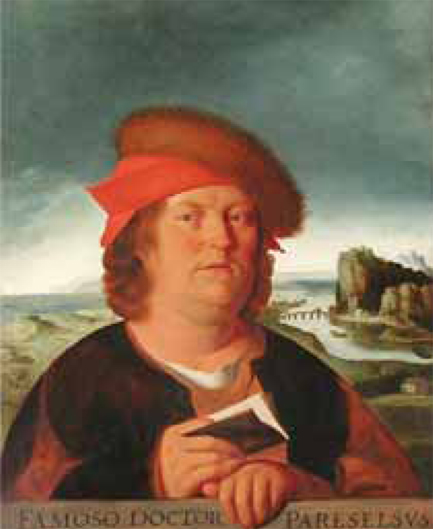
Paracelsus, właśc. Phillippus Aureolus Theophrastus Bombastus von Hohenheim (ur. 1493 lub 1494 r., zm. 1541 r.) – lekarz i przyrodnik, zwany ojcem medycyny nowożytnej
Źródło: Wikipedia
Paracelsus a piroliza
Co wspólnego z procesem pirolizy tworzyw może mieć wspólnego żyjący w XVI wieku szwajcarski przyrodnik i jaka to mądrość może nam pomóc w technologii? Paracelsus badał wiele substancji chemicznych pod kątem wykorzystania ich jako leki i jako trucizny. Jest autorem słynnej wypowiedzi: Cóż jest trucizną? Wszystko jest trucizną i nic nie jest trucizną. Tylko dawka czyni, że dana substancja nie jest trucizną. Gdy przyłożymy to twierdzenie do naszej sytuacji i uznamy że: odpady tworzyw sztucznych są „trucizną” dla instalacji pirolitycznych lub krakingowych, to rozwiązanie nasuwa się samo – trzeba zmniejszyć stężenie tworzyw we wsadzie na instalację pirolizy.
Ale czym rozcieńczyć tworzywa?
Oczywiście frakcjami węglowodorowymi, które i tak są kierowane na kraking czy pirolizę!
Czy tworzywa się rozpuszczają we frakcjach ropopochodnych?
Praktycznie wszystkie tworzywa rozpuszczają się w węglowodorach w temperaturze ich topnienia.
Jakie stężenie tworzywa we frakcji będzie bezpieczne dla procesu?
Sprawdźmy najpierw, jakie stężenia są możliwe do uzyskania: Rocznie w Polsce przetwarza się 28 mln ton ropy naftowej. Podaż odpadów z tworzyw sztucznych do zagospodarowania to rocznie 1,45 mln ton (dane z 1. części cyklu). Gdyby całe tworzywo odpadowe rozpuścić w całej ropie naftowej przetwarzanej w Polsce, to otrzymalibyśmy stężenie ok. 5%. Jest to na tyle mało, że nie trzeba by istotnie zmieniać parametrów przetwórczych w większości procesów termicznych w rafineriach.
Mimo to trzeba konieczne byłoby zbudowanie instalacji sortującej, osuszającej i rozpuszczającej na gorąco odpady tworzyw we frakcji węglowodorowej. Konieczne jest również zastosowanie dokładnej filtracji roztworu, aby oddzielić zanieczyszczenia mineralne.
Cała ta wyżej opisana „technologia” to niestety czysta technologiczna spekulacja. Nic mi nie wiadomo, aby ktokolwiek w Polsce się takim procesem zajmował. A przecież konieczne jest zbadanie wszystkich aspektów tej technologii – czy przypadkiem nie pojawią się jakieś negatywne skutki uboczne.
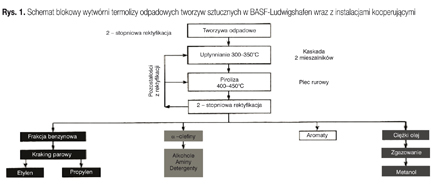
Aspekt ekonomiczny
Sprawdźmy jeszcze, czy zajmowanie się recyklingiem przez rafinerie byłoby dla nich korzystne finansowo? W dniu pisania tego artykułu (wrzesień 2015 r.) baryłka (159 l) surowej ropy naftowej kosztuje ok. 46 dolarów netto. W przeliczeniu na polską walutę daje to ok. 1,24 zł/kg surowca do produkcji tworzyw sztucznych. Koszt pozyskania odpadu z tworzyw sztucznych wstępnie posortowanego to ok. 0,25–0,30 zł/kg. Szacunkowe koszty przygotowania odpadu do postaci możliwej do zaakceptowania przez instalację pirolizy (lub innej technologii obróbki termicznej) to koszt rzędu 0,50–0,70 zł/kg.
Można więc wyliczyć, że koszt wsadu na instalacje pirolizy wahać się będzie w granicach 0,75–1,00 zł. Oznacza to dodatkowy zysk 0,24–0,49 zł na każdym kilogramie tworzywa przerobionego zamiast ropy. Jak wstępnie podaliśmy, w Polsce rocznie należałoby poddać recyklingowi 1,45 mln ton tworzyw. Oznacza to ok. 350–700 mln zł rocznie dodatkowego zysku. Jeżeli zaś ropa ponownie zdrożeje do poziomu 100 $ za baryłkę (o czym marzy Putin), zysk z takiego rozwiązania będzie oscylował w granicach 2,540– 2,90 mld zł rocznie!
Myślę, że tak wysokie kwoty warte są tego, aby podjąć przynajmniej prace koncepcyjne na temat recyklingu w rafinerii.
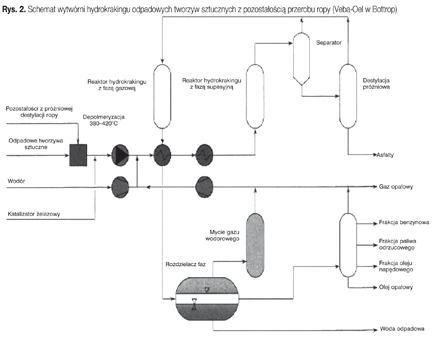
Kooperacja z rafinerią
U naszych zachodnich sąsiadów opracowano przynajmniej dwie technologie pirolizy tworzyw, pracujące w ścisłej kooperacji z innymi instalacjami rafineryjnymi czy petrochemicznymi:
1. Termoliza według technologii BASF
W koncernie BASF w Ludwigshafen (RFN) opracowano i zbudowano instalację pirolizy odpadowych tworzyw sztucznych. Współpracuje ona z innymi instalacjami, które przetwarzają z krakingu, co zilustrowano na rysunku poniżej. Sam proces pirolizy jest dwustopniowy: w pierwszym przeprowadza się upłynnianie sztucznych w dwóch kaskadowo zainstalowanych mieszalnikach w temperaturze 300–350°C. Już tu następuje częściowa degradacja polimerów z wydzielaniem chloru i chlorowodoru powstającego – między innymi – z pirolizy polichlorku winylu. Zasadniczy kraking w temperaturze 400–450°C przebiega w ramach drugiej operacji w reaktorze rurowym. Wytrącający się w koks jest okresowo wypalany mieszaniną powietrza z parą wodną. Produkty pirolizy poddaje się dwustopniowej rektyfikacji, której głównymi produktami są frakcje: benzynowa i oleju napędowego. Pozostałość destylacyjna bywa zawracana do rozpuszczania odpadowych tworzyw sztucznych i ich pirolizy. Z frakcji benzynowej ekstrahuje się aromaty przy użyciu n-metylopirolidonu, tak jak w PKN Orlen (ekstrakcja aromatów). Z kondensacji produktów pirolizy wydziela się również ?-olefiny, będące wartościowym substratem do produkcji alkoholi, amin i detergentów.
2. Hydrokraking odpadowych tworzyw sztucznych według Veba-Oel
Istota tej technologii stanowi rozwinięcie procesu katalitycznego upłynniania węgla metodą Bergiusa z lat 30. ubiegłego stulecia. Wówczas rozpylony węgiel mieszano z olejem powrotnym i katalizatorem żelazowym, aby następnie w czterech reaktorach szeregowych przeprowadzić hydrokraking substratu z wodorem pod ciśnieniem 35 MPa i w temperaturze 480ºC, reakcję powstania benzyn oraz olejów napędowych. Schemat procesu hydrokrakingu odpadowych tworzyw sztucznych wspólnie z ciężką pozostałością z przerobu ropy ilustruje rys. 2. Najpierw tworzywa sztuczne poddaje się depolimeryzacji w ciężkim oleju z przerobu ropy w temperaturze 380–420ºC. Następnie mieszanina ta, uzupełniona o rozpylony katalizator żelazowy oraz wodór przepływa do suspensyjnego reaktora hydrokrakingu, eksploatowanego pod ciśnieniem 20 MPa i w temperaturze 480ºC. Stąd mieszanina pokrakingowa przepływa do gorącego separatora. Opary i wodór kierowane są do reaktora hydrokrakingu w fazie gazowej na stacjonarnym katalizatorze niklowo-wolframowym. Natomiast faza ciekła z gorącego separatora przepływa do próżniowej kolumny rektyfikacyjnej. Jej pozostałość to asfalty, a produkt ze szczytu kolumny kierowany jest do reaktora hydrokrakingu w fazie gazowej. Stąd mieszanina poprodukcyjna kierowana jest do separatora. Wodór poprodukcyjny poddawany jest oczyszczaniu, a następnie po połowie zawracany do procesu i do sieci gazów opałowych dla lokalnej elektrociepłowni. Natomiast faza ciekłych węglowodorów przepływa z separatora do kolumny rektyfikacyjnej. Tu wydziela się frakcje: benzyna, paliwa silników odrzutowych (nafta), olej napędowy i olej opałowy. Wytwórnia o mocy 200 tys. t rocznie znajduje się w Bottrop (RFN) i stanowi instalację demonstracyjną dla jej powielania również w innych krajach.
A w następnym numerze zobaczymy, czy odpadów z tworzyw sztucznych nie da się w rafinerii wykorzystać do innych celów technologicznych niż tylko piroliza?
Jerzy Żelaziński
Nowoczesna Gospodarka Odpadami 3-4/2015