Pianka poliuretanowa to popularny materiał izolacyjny w budownictwie. Podczas jej produkcji powstają jednak odpady, których z różnych względów nie opłaca się ponownie wykorzystywać do wyrobu pianki PUR. Można ich za to użyć do produkcji płyt izolacyjnych, także do zastosowania do celów budowlanych.

Partia płyt wyprodukowana podczas próby technologicznej
Odpadowe surowce termoplastyczne
Tworzywa sztuczne w stosunku do innych tradycyjnych materiałów cechują się krótką żywotnością i szybko stają się odpadem. Ich los kończy się na wysypisku śmieci, gdzie na ogół zostają poddane segregacji. W wyniku tej operacji wydzielone zostają wszelkie opakowania z tworzyw syntetycznych, które są zróżnicowane zarówno pod względem składu, jak i jakości.
Jakość odpadów termoplastycznych jest różna w zależności od miejsca ich powstawania. Ich odzysk na drodze segregacji odpadów komunalnych wymaga szczególnie dużych nakładów na oczyszczanie i sortowanie. Sprawa czystości i jakości tych samych odpadów przedstawia się diametralnie odmiennie w przypadku powstawania ich u samego źródła, czyli u producenta tworzyw sztucznych.
Każda z metod recyklingu poszczególnych rodzajów odpadowych tworzyw sztucznych posiada oprócz zalet i wady, które przesadzają o dalszym kierunku ich zagospodarowania.
W przypadku recyklingu surowcowego, który polega na ich najkorzystniejszym przetwarzaniu aż do pozyskania surowców, z których te materiały i wyroby są wytworzone, bardzo ciekawym kierunkiem jest wykorzystanie tych odpadów do produkcji nowych wyrobów.
Produkcja nowych wyrobów w oparciu o surowce pozyskane w drodze ich recyklingu ma sens pod warunkiem, że przyszli recyklerzy lub też przemysł będą mieli dostęp do odpowiednich technologii, które pozwolą na produkcję wyrobów mogących konkurować z wyrobami wytworzonymi z surowców pełnowartościowych.
Przemysł tworzyw drewnopochodnych wydaje się być tu być branżą wręcz uprzywilejowaną, jeśli chodzi o zagospodarowanie tych odpadów. Przesądzają o tym następujące względy:
- postać odpadów tworzyw sztucznych jest podobna lub zbliżona do postaci surowca drzewnego do produkcji płyt aglomerowanych,
- urządzenia stosowane w przemyśle tworzyw drzewnych w większości przypadków umożliwiają przetwarzanie odpadów tworzyw sztucznych i odpadów tkanin syntetycznych,
- możliwość zastosowania podobnych lub zbliżonych rozwiązań technicznych, w tym doboru maszyn, urządzeń i parametrów technologicznych.
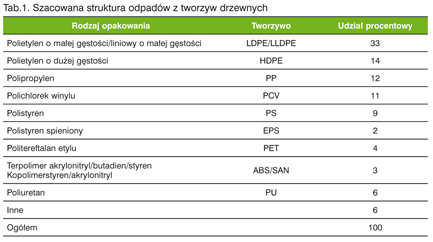
Pianka poliuretanowa i kierunki recyklingu
Pianka poliuretanowa jako produkt pierwotny powstaje w wyniku zmieszania w odpowiednich proporcjach dwóch różnych składników chemicznych. Do syntezy pianek poliuretanowych stosuje się prawie wyłącznie aromatyczne izocyjaniany oraz substancje zwane poliolami. Produkcja pianek poliuretanowych polega na tym, że ciekła mieszanka surowca o gęstości ok. 1000 kg/m3 w wyniku reakcji chemicznej zwiększa swą objętość nawet 60-krotnie, tworząc przy tym strukturę komórkową i staje się tworzywem o odpowiednich właściwościach fizyczno-mechanicznych. Pianki PU wszystkich rodzajów otrzymuje się w wyniku spontanicznej reakcji między oboma wcześniej wspomnianymi grupami ciekłych reagentów. Reakcję tę prowadzi się zwykle w temperaturze pokojowej, dodając do procesu spieniania zmniejszające palność kompozycje antypirenowe (DBBD). Reakcję dodatkowo przyspiesza się katalizatorami, którymi są najczęściej trzeciorzędowe aminy. Gotowe wyroby są utrwalane przez dodatek środków stabilizujących. Cały proces trwa około 2 minut. W efekcie reakcji chemicznej zachodzącej bardzo szybko i z wydzieleniem dużych ilości ciepła powstaje nowy produkt stały, tj. sztywna pianka poliuretanowa, o strukturze porowatej składającej się z komórek litego poliuretanu otaczającego pęcherzyki gazu (przeważnie dwutlenku węgla), bardzo lekka i o bardzo dobrych właściwościach termoizolacyjnych.
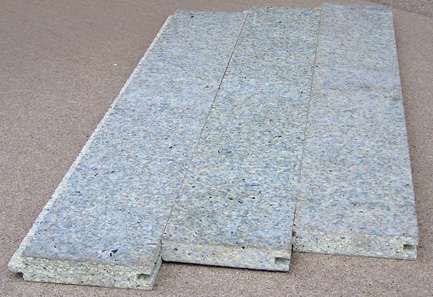
Płyty z łączone frezem na łącze pióro-wpust
Pianki o porach zamkniętych są stosowane do wyrobu pływaków, podkładek amortyzacyjnych, izolacji cieplnych i akustycznych. Pianki z porami otwartymi są używane do wyrobu gąbek, poduszek laminowanych warstw do ocieplania odzieży, w tapicerce itp. Istnieje przy tym możliwość otrzymania pianki na placu budowy, co pozwala wykonać stosunkowo cienkie i szczelne izolacje cieplne dachów metodą natrysku kilkucentymetrowej warstwy.
Sztywne pianki konstrukcyjne stosuje się do wypełniania pustych przestrzeni w konstrukcjach budowlanych, drzwiach i ramach okiennych, do wyrobu izolacyjnych płyt konstrukcyjnych, wyposażenia kabin statków i samolotów. W Polsce poliuretanowe tworzywa piankowe produkowane są pod nazwą Izopur.
Odpady produkcyjne pianki poliuretanowej w postaci wypływów technologicznych, odpadów zmieszanych PUR i HDPE powstają podczas procesu piankowania (wtrysku pianki poliuretanowej w formy rur i innych elementów armatury ciepłowniczej) oraz z wyniku końcowej kontroli jakości wyrobów. Odpady te posiadają te same właściwości, co pianka poliuretanowa pozostająca w wyrobach, tj.:
- niską nasiąkliwość i wymywalność zanieczyszczeń,
- odporność na rozpuszczalniki, rozcieńczone kwasy i inne chemikalia,
- brak w składzie formaldehydu,
- brak emisji do atmosfery niebezpiecznych substancji,
- brak zapachu i nieszkodliwość fizjologiczna,
- odporność na mróz, butwienie, gryzonie, gnicie i na korzenie,
- brak oddziaływania korozyjnego na izolowany materiał (stanowi zwykle osłonę antykorozyjną),
- nieszkodliwa dla zdrowia i przyrody.
Możliwości ponownego przerobu na nowe materiały płytowe
Produkcja materiałów izolacyjnych z pianki poliuretanowej jest technologią znaną i popularną, stosowaną zarówno w Europie, jak i na świecie. Sam produkt w postaci wielu odmian znalazł szerokie zastosowanie w różnych gałęziach przemysłu, które jednocześnie są źródłem powstawania tych odpadów. Materiały izolacyjne wykonane z pianki poliuretanowej nie należą do wyrobów tanich, a samo przetworzenie odpadów na półprodukty do nowych produktów jest z ekonomicznego punktu widzenia jest obecnie mało opłacalne. Przyczyną takiego stanu rzeczy jest brak efektywnych i sprawdzonych metod przerobu na nowe wyroby lub półprodukty do syntezy nowych wyrobów.
Próby spajania za pomocą temperatury czy też spoiw syntetycznych są procesem drogim albo mało efektywnym. Poza tym należy uświadomić sobie, iż z materiału recyklingowego nie uda się wytworzyć nowego materiału o takich samych parametrach i właściwościach. Chcąc wytworzyć z odpadów pianki poliuretanowej płytę o izolacyjności takiej jak przemysłowa zawsze trzeba będzie zużyć więcej surowca. Oznacza to, że uzyskanie wysokich współczynników izolacyjności (na poziomie wyrobu pełnowartościowego) jest możliwe głównie przy zwiększeniu gęstości wyrobu. Dzieje się tak, ponieważ odpady pianki przed ponownym przerobieniem muszą zostać poddane ujednoliceniu wymiarowemu, a to oznacza, że zamknięta struktura pęcherzyków pianki poliuretanowej zostanie w znaczącej mierze uszkodzona i staną się one przepuszczalna dla ciepła.
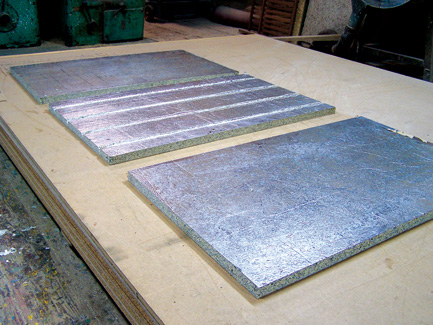
Płyty z kanałami na przewód grzewczy
Im mocniej rozdrobniona zostanie pianka poliuretanowa, tym bardziej w dalszych etapach produkcyjnych trzeba będzie zwiększać odpowiednio gęstość płyt, aby wytworzyć materiał o izolacyjności zbliżonej do odpowiednika produkcyjnego oraz niskiej wartości nasiąkliwości.
Dodatkowo trzeba sobie zdawać sprawę, że stopień rozdrobnienia będzie miał bezpośredni wpływ na ilość lepiszcza zużywanego w celu powiązania rozdrobnionych cząstek w arkusz płytowy lub blok. Z kolei ilość lepiszcza oraz jego rodzaj w znaczący sposób będzie wpływał na wielkość współczynnika izolacyjności wytworzonych płyt.
Użycie tanich żywic mocznikowo-formaldehydowych będzie zdecydowanie obniżać poziom izolacyjności płyty. O wiele lepszy efekt daje zastosowanie klejów poliuretanowych do spajania cząstek pianki poliuretanowej - izolacyjność poprawi się istotnie, ale też koszty wytwarzania nowego wyrobu będą wyższe.
Przygotowanie pianki do przerobu
Większość operacji, jakie trzeba będzie przeprowadzić w celu wytworzenia nowego materiału płytowego, można przeprowadzić w sposób analogiczny jak przy produkcji płyt wiórowych. Zbieżność podobieństwa pewnych operacji pozwala na zaadoptowanie niektórych maszyn i urządzeń do tego procesu.
Rozdrabniając piankę pozyskaną z recyklingu w sposób kontrolowany tak, aby uzyskać odpowiednie średnice ziaren z jednoczesnym zachowaniem odpowiedniej proporcji cząstek umownie zwanych „dużymi” do cząstek „małych” można wytworzyć w procesie ich spajania materiał płytowy o dobrych właściwościach izolacyjnych i jakościowych.
Sam proces rozdrabniania pianki poliuretanowej jest jedną z ważniejszych operacji technologicznych, a sposób jego przeprowadzenia ma decydujący wpływ na własności izolacyjne nowo wytworzonych materiałów. Sposób rozdrabniania wraz z prawidłowym doborem parametrów tego procesu musi doprowadzić do powstania mieszaniny cząstek z odpowiednio wysoką ilością zamkniętych pęcherzyków, które będą decydowały o dobrej izolacyjności nowo wytworzonego wyrobu.
Na podstawie licznych prób przeprowadzonych w warunkach laboratoryjnych i przemysłowych najbardziej odpowiednią metodą rozdrabiania zróżnicowanych postaciowo odpadów pianki poliuretanowej wydaje się być metoda działająca na zasadzie cięcia nożowego. Przeprowadzone próby rozdrabniania tego surowca na urządzeniach laboratoryjnych i przemysłowych wykazały, że metoda ta pozwala w miarę płynnie sterować jakością i ilością otrzymywanych cząstek.
Sam proces rozdrabniania odpadów kawałkowych pianki do postaci cząstek o przydatnej charakterystyce jest procesem stosunkowo prostym, a sam przebieg procesu rozdrabniania w ogólnym zarysie jest następujący.
Odpady kawałkowe poprzez zasyp trafiają do komory mielenia. W komorze znajduje się głowica, na której osadzone są noże wirujące. Tną one zasypany surowiec w momencie, gdy noże wirujące przetną linie styku osi noży stałych. Odległość noży stałych od linii styku noży wirujących jest wielkością nastawną i jest to pierwszy stopień regulacji wielkości otrzymywanych cząstek. Cięcie zasypanego surowca trwa do momentu, aż osiągnie on takie wymiary, że będzie mógł wydobyć się poprzez otwory znajdujące się w sitach sortujących. Sita te stanowią drugi stopień regulacji wielkości wytwarzanych cząstek.
Opis technologii właściwości płyt
Proces wytwarzania arkuszowych materiałów izolacyjnych z odpadów pianki poliuretanowej rozpoczyna się od operacji rozdrobnienia surowców odpadowych do żądanej postaci według wyżej opisanej metody. Parametry rozdrabniania powinny być dobrane tak, aby w następstwie tego procesu uzyskać mieszaninę cząstek, w której zostanie zachowana odpowiednia proporcja pomiędzy cząsteczkami „dużymi” oraz „średnimi” a „drobnymi”.
Kolejna operacja, która w zasadzie może przebiegać równolegle do pierwszej, polega na rozdrobnieniu odpowiednio dobranych do tego celu termoplastów, pochodzących z selekcji odpadów opakowań spożywczych. Podobnie jak w przypadku pianki poliuretanowej, proces rozdrabniania powinien przebiegać według tej samej metody. Jednakże tu parametry rozdrabniania powinny być tak dobrane, aby wytworzyć mieszaninę o drobnych cząstkach, które w dalszym procesie prasowania na gorąco wytworzą szereg licznych i trwałych połączeń.
Na potrzeby tej technologii można wykorzystywać również tkaniny, wykładziny, materiały syntetyczne itp., które należy doprowadzić w procesie rozdrabniania do postaci włókien lub strzępków.
Po wymieszaniu w odpowiednich proporcjach poszczególnych składników, tj. pianki oraz termoplastów (pod różną postacią) ma miejsce wstępne uformowanie kobierca na blasze obiegowej i następnie jego zagęszczanie w prasie wstępnej. Uformowane i wstępnie zagęszczone kobierce zostają umieszczone pomiędzy półkami prasy gorącej. Przy ściśle określonej temperaturze oraz doborze krzywej prasowania umieszczony wsad w prasie zostaje zaprasowany do określonej grubości. Ze względu dużą adhezję termoplastów do płaszczyzn stykowych, w procesie prasowania na gorąco stosuje się specjalne środki do zabezpieczenia powierzchni.
Po wyprasowaniu płyty poddaje się klimatyzacji, a następnie formatyzowaniu na odpowiedni wymiar.
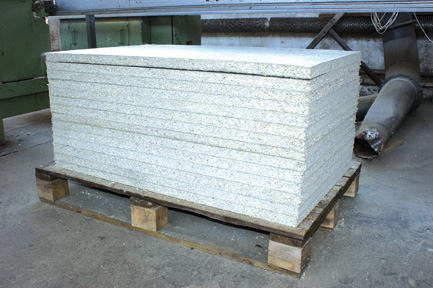
Wyprodukowane płyty na palecie
Możliwości zastosowań nowego produktu
Przedstawiona technologia daje szerokie możliwości sterowania właściwościami wytwarzanych płyt. W zależności od postaci użytych surowców, ich wzajemnych proporcji oraz doboru parametrów techniczno-technologicznych można uzyskać szeroką gamę płytowych materiałów o ukierunkowanych właściwościach i zastosowaniu.
Przy doborze odpowiedniego sposobu rozdrabniania i odpowiednich termoplastów można z powodzeniem wytworzyć materiał o dobrych parametrach izolacyjnych.
Zmieniając postać pianki poliuretanowej oraz jej udział względem innych składników możemy wytwarzać płytę o dobrych parametrach mechanicznych, z zachowaniem dobrego współczynnika izolacyjności cieplnej i niskiej nasiąkliwości.
Płyt te można łatwo obrabiać mechanicznie, frezować na tzw. pióro-wpust i łączyć w duże powierzchnie. Można je też prasować, nadając im odpowiednie cechy i formę. Wytworzone płyt można w łatwy sposób zaadoptować jako izolację do systemu ogrzewania podłogowego.
Leszek Danecki
Ośrodek Badawczo-Rozwojowy Przemysłu Płyt Drewnopochodnych w Czarnej Wodzie
Zbigniew Paluchewicz
Instytut Mechanizacji Budownictwa i Górnictwa Skalnego
Centrum Gospodarki Odpadami w Katowicach
Nowoczesna Gospodarka Odpadami 2(2) 2013